Medical CNC Machining
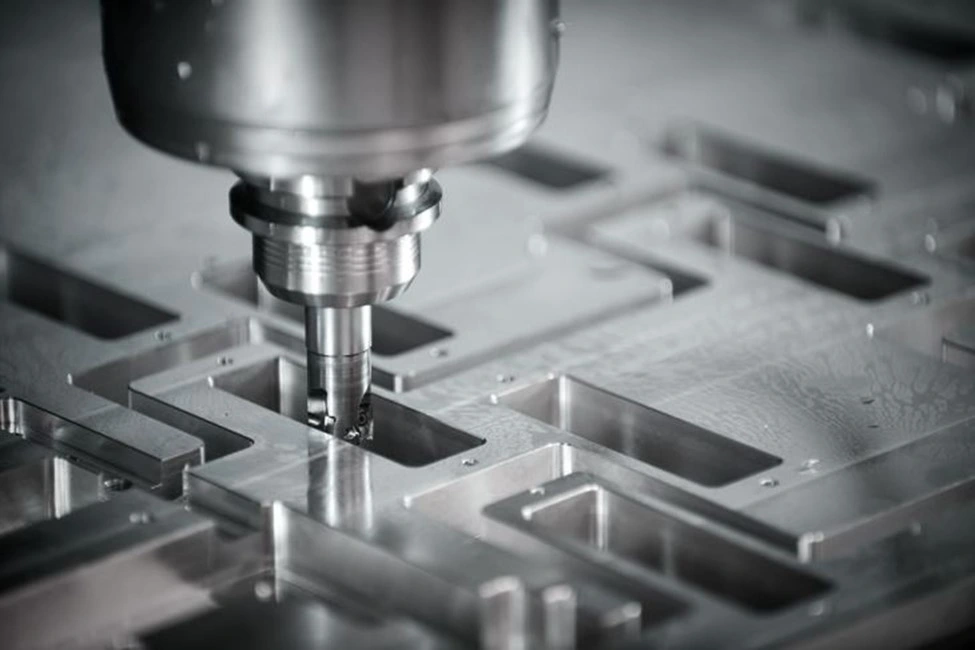
The applications of CNC machining in the medical field are vast and diverse. From creating intricate components for surgical instruments to manufacturing parts for imaging equipment, Swiss Machining Inc. has been at the forefront of this innovation. Our portfolio includes high-precision parts for orthopedic implants, dental instruments, and life-supporting devices, showcasing our versatility and technical prowess.
Precision is paramount in the medical field, where a fraction of a millimeter can determine the success of a surgical procedure or the functionality of a medical device. CNC machining offers unparalleled precision, repeatability, and speed. Swiss Machining Inc.’s CNC technology ensures that each part meets stringent medical standards, contributing to safer, more reliable medical care.
At Swiss Machining Inc., we utilize a variety of biocompatible materials for medical devices, including stainless steel, titanium, and PEEK. These materials are chosen for their strength, durability, and compatibility with the human body. Our expertise in material science allows us to select the perfect material for each application, ensuring optimal performance and safety.
Our approach at Swiss Machining Inc. is defined by precision, innovation, and quality. We employ advanced CNC machines equipped with the latest technology to meet the exacting standards of the medical industry. Our team of skilled engineers and machinists are experts in designing and producing complex parts, while our stringent quality control processes ensure each product meets regulatory requirements.
The medical industry is in a constant state of evolution, and so are the technologies in CNC machining. Swiss Machining Inc. stays ahead of the curve by incorporating advancements such as 5-axis machining and real-time monitoring to enhance precision and efficiency. We are also exploring the integration of AI and IoT in our manufacturing processes to further push the boundaries of what's possible in medical device manufacturing.
The challenges in medical CNC machining are complex, ranging from adhering to strict regulatory standards to managing intricate design requirements. Swiss Machining Inc. tackles these challenges head-on through meticulous planning, advanced technology, and a deep understanding of the medical industry's needs.
In the medical field, precision is not just a desirable trait; it is an absolute necessity. Surgical procedures, diagnostic equipment, and life-sustaining devices all demand components that meet stringent specifications. CNC machining, with its ability to achieve remarkable precision, has become the cornerstone of medical device manufacturing

The applications of CNC machining in the medical field are diverse and impactful. One of the primary areas where Swiss Machining Inc. excels is in the production of components for surgical instruments. These instruments require intricate and precisely manufactured parts to ensure the success of delicate surgical procedures. CNC machining allows us to create components with complex geometries and tight tolerances, meeting the exacting requirements of surgical instruments.
Additionally, Swiss Machining Inc. plays a crucial role in the manufacturing of components for imaging equipment used in medical diagnostics. From CT scanners to MRI machines, the precision of the components is directly linked to the accuracy of the diagnostic results. Our CNC machining capabilities contribute to the production of high-quality components that enable medical professionals to make accurate and timely diagnoses.
Orthopedic implants, another vital aspect of medical treatment, also benefit from the precision of CNC machining. The design intricacies of implants, coupled with the need for biocompatible materials, make CNC machining the ideal choice for their production. Swiss Machining Inc. has been a key player in this arena, providing orthopedic surgeons with reliable and precisely manufactured implants.
Dental instruments represent yet another facet of our expertise in medical CNC machining. The intricate nature of dental tools requires manufacturing techniques that can produce small, detailed parts with exceptional precision. CNC machining fulfills this requirement, enabling us to contribute to the dental industry’s ongoing advancements in patient care.
Life-supporting devices, ranging from infusion pumps to respirators, also rely on CNC-machined components. The reliability and precision of these components are paramount to the overall functionality and safety of these critical medical devices. Swiss Machining Inc. is proud to be a trusted partner in the production of components that contribute to enhancing and saving lives.
The advantages of precision machining in the medical sector are manifold. The first and most significant advantage is the unparalleled level of precision that CNC machining can achieve. In medical applications, where accuracy is non-negotiable, this capability ensures that every component meets the exact specifications required for its intended purpose.
Repeatability is another crucial advantage offered by CNC machining. Consistency in manufacturing is paramount in the medical field, where deviations from specifications can have severe consequences. Swiss Machining Inc.’s CNC technology ensures that every part produced is an exact replica of the approved design, providing the reliability necessary for medical devices.
Speed is also a notable advantage of CNC machining. While precision and repeatability are maintained, the efficiency of the manufacturing process is significantly improved compared to traditional manual methods. This allows Swiss Machining Inc. to meet the demands of the rapidly evolving medical industry, where time is often a critical factor in bringing new technologies to market.
The ability to work with a variety of materials is a further advantage of precision machining. In medical CNC machining, the choice of materials is critical, considering factors such as biocompatibility, strength, and durability. Swiss Machining Inc.'s expertise in material science ensures that the most suitable material is selected for each application, contributing to the overall performance and safety of the final products.
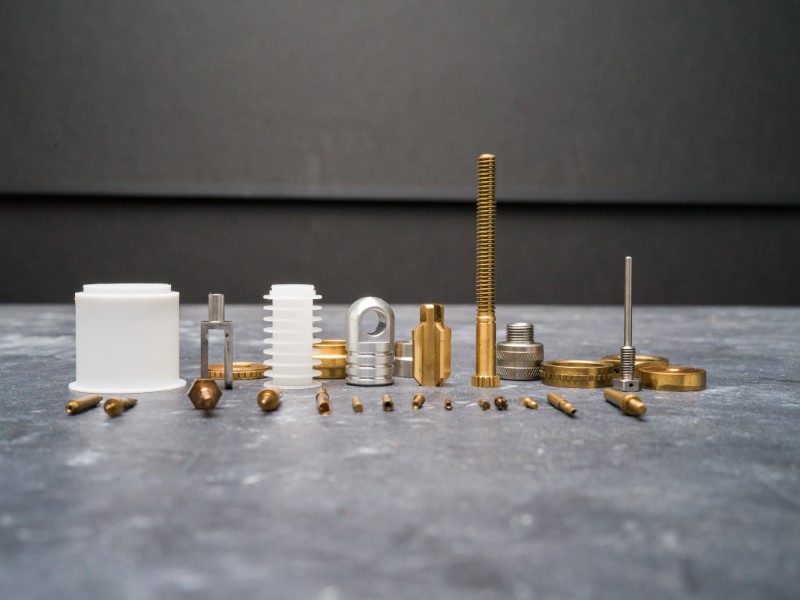